We have a very extensive range of tube end forming tooling and machines covering bespoke forms as well as standard flaring and beading forms such as ORFS, Triple-Lok and Walform, and we can supply and/or fit all the relevant fittings as well as standard hydraulic and pneumatic end fittings, nuts and rings, ex stock, either loose, or assembled to DIN 2353. With a strong background in fluid transfer, we are very familiar with providing end forms and fittings that will allow you to achieve leak-free systems.
We will usually have something suitable or adaptable to your needs, but if not, we can produce new tooling to suit. We can also provide machined hose-tail ends on our tubes suitable for lower pressure hose connection applications.
If you needed to perform mechanical fixing of your tube, or tube-to-tube assembly, we offer a variety of suitable ends forms, such as notching, mitre cutting or flattening.
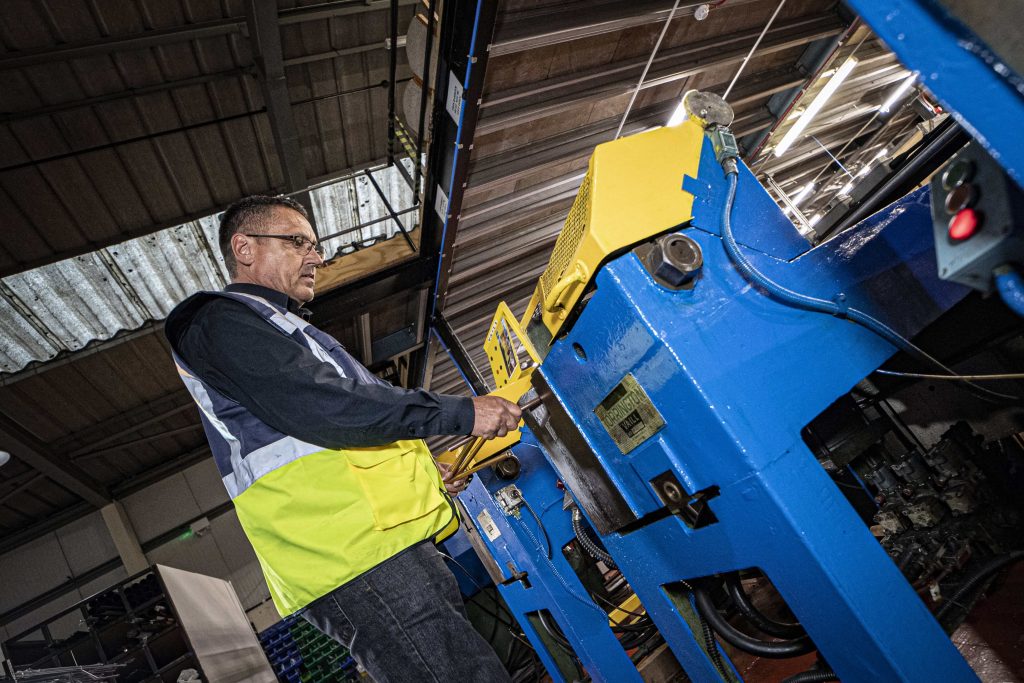
Notching, also known as fish-mouthing, or cod-mouthing, creates a scalloped-out shape on the end of the tube, so that it neatly fits around another tube. This can then be welded or brazed in place, a service that we can offer, or you can perform during your production process. If you want to use a notched end but make it semi-permanent it is possible to weld a nut inside the notched end and drilling a hole through the other tube. A bolt can then be passed through the hole and screwed into the nut. This is often used in furniture joints.
Mitre cutting is, quite simply, cutting an angle on the end of the tube. This can be very useful in tube construction projects, and we can cut the tubes with a high accuracy and repeatability. Where required, especially for compound angles, we will produce bespoke cutting jigs.
Tube flattening may be necessary for a variety of structural applications, and we can also drill holes through the flattened sections if you intend to bolt two or more tubes together at this point.
Another common tube jointing system, where one tube is pushed into another, makes use of either swaging or expanding the tube ends. We can offer both approaches, giving you complete flexibility in your designs. These joints can either be temporary, or for assembly by your end customer, or can be brazed or welded, either by us or by you.
Of course, we also offer threading on the end of tubes. Both internal thread and external thread options are available. There can be challenges with thread forms due to requiring a suitable wall thickness and the difficulty of tapping or cutting a thread if it has to be done after the tube is bent. As always, we would encourage you to discuss these options with us before your design is set. Often, attaching a threaded end fitting, using a standard end form mentioned in the first paragraph, may be a more cost-effective solution.
If you are producing any form of manifold, then threading the stub pieces on one end may be a good solution, especially in conjunction with our facility to produce tapped holes in the main tube wall using a process known as flow drilling. This creates a material boss that allows enough thread turns to be tapped to provide secure connections.
All of these solutions and applications are explained fully in our Tube End Design Guide available for free download from the Links tab at the top of the page.